I expect by now that anyone following this series of articles is either contemplating setting up their own kitchen installation business or wondering how to sell the expensive tools they think they invested in before the plaster fell off the walls, the pipes flooded the kitchen and the wall units collapsed.
For those of you who've already sign written the van, congratulations and for those of you filling in the "tools for sale" adverts, hang fire, replace that pen with a cordless drill and don't give up so easy.
Right Angle Cordless Drill
Choosing the right base units
Base units come in various configurations and are available in flat pack or rigid format. Board thickness, construction methods and accessories also highlight the differences between manufacturers. The majority have adjustable legs fitted for ease of fitting and to prevent water ingress.
Speaking as a former installer my personal choice for strength and longevity would be to choose a carcass of at least 18mm construction with a back of at least 9mm board thickness and metal sided soft close drawer boxes again with a solid base of at least 15mm board. Rigid units will save on installation time but otherwise carry no major advantage over flat pack units.
Many manufacturers build co-ordinated carcasses that match their door finishes. This is a useful advantage when ends are visible but as an alternative you can fit a coordinated end support panel or even a door fascia.
The majority of carcasses are constructed using melamine faced chipboard and particular care should be given to the sink base carcass which will be extremely vulnerable to water ingress over it's lifetime. To counteract this problem I have developed a product called Unitsaver. I hasten to add that I'm still waiting for the call from a cabinet manufacturer who sees the product as a great addition to their range so until then I'm afraid it isn't available to the consumer.
Tools required for the job
- Cordless screwdriver
- Hand Tools
- Jigsaw
- 5mm HSS Drill bit
- 50mm, 25mm, 30mm and 16mm screws
- Pair of clamps
- Holesaws
- Spirit level
- Tape Measure
- Power Drill
- Compass and pencil.
- Safety Equipment - Goggles, Dust Mask etc
- Extension Lead
The fitting
Fitting should commence in the corner of the kitchen. Starting at the highest point in the floor, a level line should be transferred to the walls marking the finished height of your cabinets.
Corner cabinets are generally available in two configurations, an L-shaped unit, usually 900mm width and a conventional corner cabinet available in sizes from 900mm to 1200mm. If the design allows then one, the other, or both will be suitable for your kitchen.
Adjust the legs to ensure the cabinet meets the line and, using a spirit level, adjust to ensure the unit is plumb and level. Continue the above method with all subsequent units and clamp together making sure all edges are flush and level.
To connect units together, use clamps inside the units to adjoin the units both top and bottom, ensuring that the front and top edges are flush. When clamping together protect units by using hardboard off cuts or similar behind the clamp jaws.
Remove one screw from each of the hinge back plates and rotate back plate to expose area behind. Using a 5mm wood bit, drill part way through the first carcass behind the hinge back plate and fix the two together with a cordless screwdriver using 30mm screws for 18mm units and for 25mm screws for 15mm units. Reposition back plate and fix. This will serve to conceal the fixing. If however, both units are connecting on the closing side of the doors - use the same procedure and cap the screws.
Where ends are not visible it is advantageous to cut off the service void from the bottom of the cabinets leaving 80mm of the full cabinet depth from the top of the unit. This will serve to overcome any out of true plastering behind the base units and provide an easy means of running cables behind the units after fitting.
Most manufacturers employ a service void of approximately 50mm at the back of base units and this is essential not only for plumbing and electrical services but also for scribing to the walls if necessary. To ensure that no gaps are visible where the last unit meets the wall you may need to scribe the cabinet. To do this, level the cabinet and clamp it to the adjacent one leaving it 30mm proud of the front edge, clamp the units together, set the compass to 30mm between pencil and point and run the point of the compass down the wall keeping it parallel with the pencil point. The pencil line left on the carcass will act as a guide for cutting with a jigsaw. After cutting, fit the cabinet as described above. This will leave a perfect finish to the wall.
When all the cabinets are levelled and in place, they will require fixing to the walls. This will only be required at alternate gables. Hold a 25mm right-angled bracket to the wall and against a gable interior. Mark through the bracket with a pencil to the wall and drill at a downward angle. Insert a rawlplug and fix to the wall using a 50mm screw. Fix the bracket to the cabinet gable using a 16mm screw.
Fitting appliances
An important thing to remember is, when fitting a conventional corner cabinet that has an appliance fitted on the return, to allow sufficient space for the door to open 90? and to ensure that the appliance door has clearance to open without infringing on the door handle. This may require the fitting of a corner fillet manufactured on site but will ensure that your dishes can be placed into a fully open dishwasher.
Remember to align the hob base unit with the extractor. This task takes precedence over all others for the efficient operation of the extractor. It may be necessary to reposition the corner unit but this can be amended by again utilising a filler on the corner base.
When fitting integrated appliances you will need to leave a space between cabinets. Using a straight length of wood or plinth, clamp flush to the already levelled cabinets and use this as a guide for fitting the next cabinet making sure you leave the correct space between the units and this applies to both the front and the back. This method also applies when fitting units either side of a freestanding or range cooker.
Well that's it, you're ready for the worktops, these come in a various materials, the most popular being laminate. In the next article I'll be explaining how to install your worktops and appliances.
Finally, for those of you still debating whether to call in the nearest kitchen installers, I'd like to offer some words of encouragement.
My first installation took place within the confines of Southport Zoo. I had only a variety of hand tools, a power drill, a second hand jigsaw and a strong desire to complete my first kitchen without a hitch. This I did, after three weeks.
It took me so long to complete that they installed a glass screen for visitors to view the monkey installing the kitchen.
So don't throw in the towel, don't sell the tools, put on those overalls and give it another go. It's so easy a monkey could do it.
Any questions or more information can be found on our popular kitchen buyer's forum.
next article: Fitting Kitchen Worktops
© T Foley 2009
Special Price!!! DEWALT DW960K-2 Heavy-Duty 3/8-Inch 18-Volt Ni-Cad Cordless Right Angle Drill
Nov 06, 2011 11:19:38
Click for larger image and other views
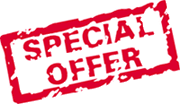
DEWALT DW960K-2 Heavy-Duty 3/8-Inch 18-Volt Ni-Cad Cordless Right Angle Drill Feature
- 2 speed ranges 0-500/0-1,500 rpm for increased user flexibility providing a wide range of applications
- 320 unit watts out of maximum power for heavy-duty applications such as turning large bits and fasteners
- Multi-grip trigger provides comfort and convenience, allowing the user to get into tighter spaces while still having access to the trigger
- variable speed and reversing gives the user the ability to control speed for greater accuracy, and the convenience of reverse
- Durable, right angle transmission with sealed ball bearing for a longer tool life;
DEWALT DW960K-2 Heavy-Duty 3/8-Inch 18-Volt Ni-Cad Cordless Right Angle Drill Overview
A unique tool that makes it easy to work in tight, awkward spaces without sacrificing power, the DW960K-2 right angle drill is a member of DeWalt's 18-volt power tool system. Featuring two distinct modes for project-specific performance, a low mode that delivers 0 to 500 RPM for 310 in./lbs. of torque and a high mode that delivers 0 to 1,500 RPM for 80 in./lbs. of torque, this heavy duty tool performs well in a wide range of applications. Also offering a 3/8-inch chuck that is compatible with a large compliment of drill bits and a multi-grip design that forefronts a three-position rubber paddle switch for maximum versatility and close quarters, this drill driver comes with a one-hour charger, two 18-volt batteries, a screwdriver bit, and a heavy-duty kit box for easy transport and storage.SAVE NOW on the special offers below!
Available In Stock. |
This DEWALT DW960K-2 Heavy-Duty 3/8-Inch 18-Volt Ni-Cad Cordless Right Angle Drill ships for FREE with Super Saver Shipping. |
Price : Click to Check Update Prices Please. |
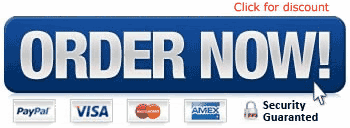